What is a dispenser appropriate for fine dispensing?
A dispenser is a generic term of devices that discharging a liquid agent, and there are various types of dispensers whose operation principles are different.
Although the structure of an air-pulse type used widely in general is simple and its maintenance performance is excellent, its air responsiveness is poor, so it cannot control the amount to be dispensed stably.
Although volume-metering types including a screw type can control the amount to be dispensed with rotation amount of the motor, it is constructed to push a regulated amount of a liquid agent from the cavity, so that it has the limited capability of a minute amount of dispensing.
Although a jet dispenser can dispense a minute drop of liquid in a nano litter (nL) level without coming in contact with a work, the liquid drop landed at the target position spreads over the work, so that the dispensed diameter is not supposed to become small easily.
The Twin-air method originally developed by Engineering-Lab has the quite different structure from those of the conventional dispensers, and it is best suited to fine dispensing allowing a very minute amount to be dispensed in a pico-litter (pL) level.
Features of each dispenser type and comparison of fine dispensing performances
№ | Dispenser type | Features and advantages | Fine dispensing performance |
---|---|---|---|
1 | Air pulse type | Simple structure and high maintaining performance Inexpensive | × (Uncontrollable) |
2 | Screw type (Volume-metering type) | Dispensing capability of a high-viscosity liquid agent Easy change of dispensing amount | △ (μL level) |
3 | Jet (Non-contact) | Non-contact dispensing and just a little affected by the clearance between a work and a dispenser No need of moving up/down of the Z-axis, and appropriate for high-speed dispensing | ○ (nL level) |
4 | Twin-air | Good at a very minute amount of dispensing Self-suck-back function for preventing a liquid agent from dripping | ◎ (pL level) |
Principle and features of the Twin-air type
A Twin-air dispenser uses the patented technology originally developed by Engineering-Lab to independently control two pneumatic lines, and then this enables dispensing to the smallest dots in the world.
Control of two pneumatic lines means that another pneumatic control unit (R-unit) is installed on the second stage between a syringe and a nozzle in addition to control of the pressure of air (compressed air) supplied to the syringe, and this realizes high responsiveness of the R-unit installed very close to the nozzle, and then enables liquid dispense excellent in controllability.
In addition, the R-unit can control the positive pressure and the negative pressure, so that it prevents liquid from dripping, cobwebbing or clipping up to the nozzle by self-such-backing (absorbing) it when the dispenser finishes dispensing. Therefore, the dispenser keeps a starting point and an end point of a dispensed line uniformly.
The strongest point of the Twin-air method is high-precision dispensing of a very minute amount of liquid agent. The minimum dispensing diameter is 40μm when the dispenser dispenses to a dot, while the minimum line width is 40μm when it dispenses to a line. The minimum discharge amount is several 10 pico-litters (pL).
Because the Twin-air dispenser can discharge up to 1,000 Pa.s high-viscosity liquid, it can support a wide variety of liquid agents such as conductive paste, UV-curing resin, polyimide and resist.
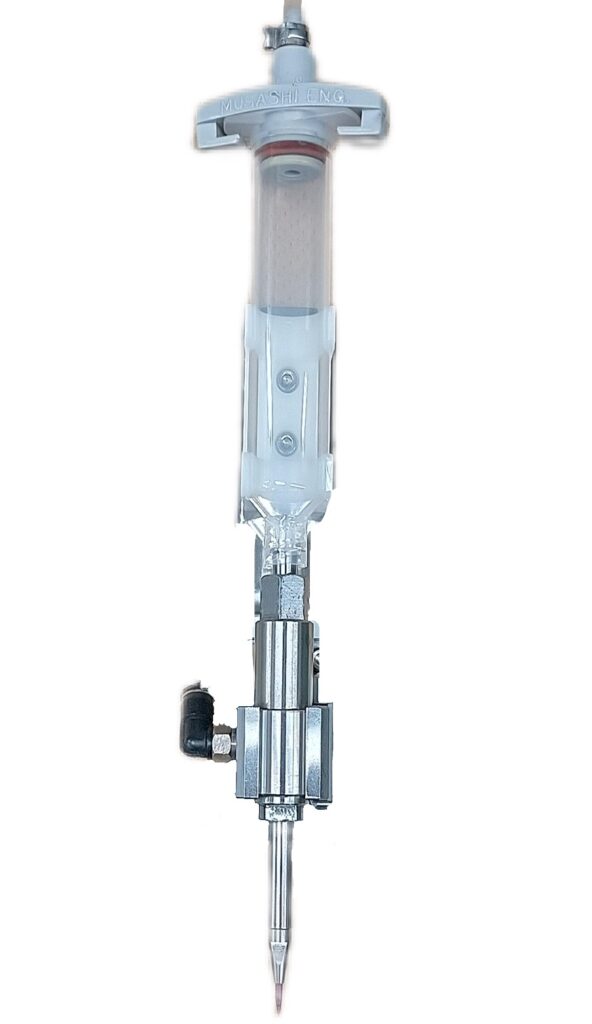
Twin-air (Basic function type)
Structure and principle of a piezojet dispenser
When clearances between each work and the dispenser is not uniform, a non-contact jet dispenser is one of the powerful options. However, a piezojet dispenser on which a piezo-actuator is mounted is the most appropriate for fine non-contact dispensing.
The structure of a piezo-actuator is simple: the rod connected to the piezo element finely deformed when voltage is applied to it repeats reciprocating motions to convey the pressure to a liquid agent inside the liquid agent chamber, and then the liquid agent is dispensed from the nozzle hole. (See the right figure.)
This actuator is supposed to be best suited to high-precision minute amount dispensing because a piezo element can repeat several 10-micron minute displacement at high-speed and accurately.
A piezo element performance also continues permanently, so that it cannot be lowered due to aged deterioration of a part unlike an air (electromagnetic) type jet dispenser, and its high-precision performance can be kept for a long time.
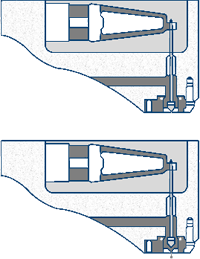
Operation principle
(Upper figure: Closed Lower figure: Discharging)
Piezojet dispenser control method
A piezojet actuator uses the CPU to digitally set parameters such as the length, speed and torque of the stroke in which the rod moves up and down when the valve opens/closes because it can control the piezo element operation with voltage correctly.
A piezojet dispenser can set a portfolio most appropriate for closing/opening a valve according to the characteristics and/or viscosity of a liquid agent as well as set the discharging amount as desired. Therefore, it can solve a problem that tends to occur at an air type jet dispenser such as generation of bubbles and scattering of liquid agent when it landed on a target.
Because generally a low-viscosity liquid agent scatters easily, you have to lower the rod moving-down speed to prevent the agent from scattering, while you have to raise the torque to be applied when the rod moves down in case of a high-viscosity liquid agent to dispense it powerfully. On the other hand, to prevent bubbles from being generated, you have to create two portfolios, one applied for when the rod moves up and another for when the rod moves down to prevent any air from being sucked by decreasing the speed at which the rod moves up.
Just one piezojet dispenser can handle various types of liquid agents from an aqueous low-viscosity liquid agent to a high-viscosity pasty liquid agent because it can create a portfolio best suited to each liquid agent.
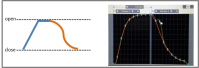
Setting a portfolio for a low-viscosity liquid
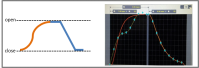
Setting a portfolio for a high-viscosity liquid
To select the most appropriate dispenser
Although both a Twin-air dispenser and a piezojet dispenser are appropriate for fine dispensing, their structures and features are different from each other. Therefore, you have to select the most appropriate dispenser by considering many items such as the target amount to be dispensed, the liquid characteristics (viscosity), work shape and tact time (number of dispensed positions per second).
To dispense to a minute area, a Twin-air is the best choice because it can dispense to the smallest area in the world. However, it has several restrictions: viscosity of a liquid agent and diameter of a filler, so you have to check the physical properties of the liquid agent you are to use. The work shape is also an important factor for choice. When a work is warped or it has any cavity, check to see if a nozzle can approach it or not. Then select a Twin-air (contact type) or a jet type (non-contact type).
Select the most appropriate dispenser by considering the productivity (tact time). It is recommended to verify your selection with using the liquid agent and/or work you are to use actually. Twin-air dispensers and piezojet dispensers are always prepared at our Technical Center (Matsumoto City, Nagano) and Shinagawa Showroom (Tokyo) so that we can use the liquid agent/work the customers provided with to run the corresponding verification tests.
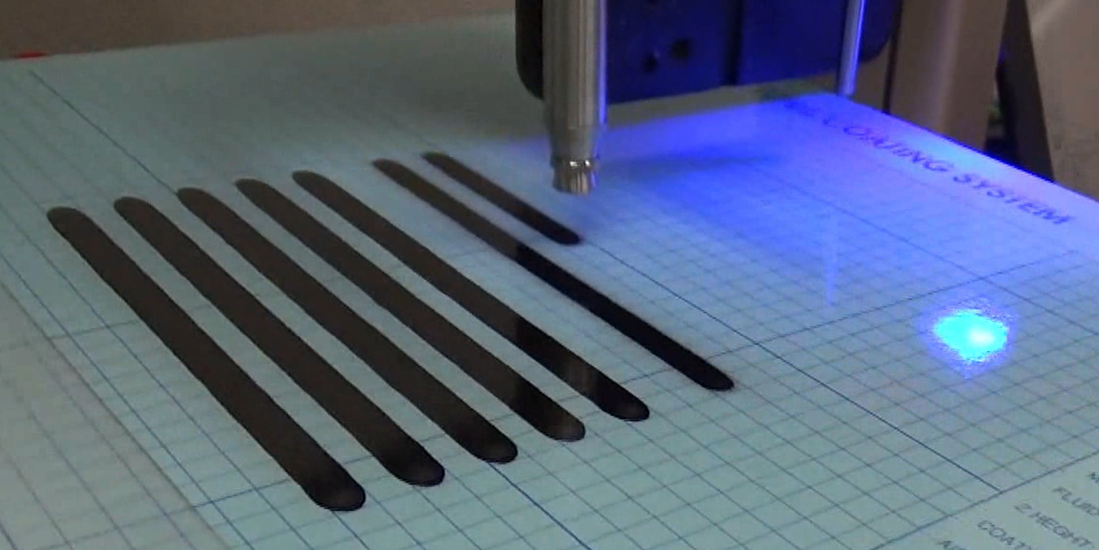